M3: Machine – Mass – Mold
DESIGN: Lotte Schloer
Germany
make me! 2020
The mass product and the unicum embody two poles in the intersection of design, arts, and craftsmanship. What separates the “perfect“ duplicate of the “imperfect“ unicum? It is the developing process whose steps I am exploring. In my thesis, I developed a self-built pressure-casting machine that allows for small series productions in an experimental design environment. I created a new type of mold: the rotatable plaster mold with which a pattern is cut into both parts of the form – the rotation of the halves creates infinite variations of the original pattern. The form spawns an – oxymoronically – industrial unicum. Crossing borders between design, art and craft, controlling the process is crucial to be: Only if I can intervene at every step, I determine the result being craft, art or design. Moving from experimental approaches to use cases, I discovered that the Rotatable Mold is not only useful for decorating plates but also for, e.g., sieves with different sizes of meshes. Likewise, handles or spouts can be mounted in various positions without using different molds. This is particularly relevant when individualizing products, for example, for people with special needs.
In times of cheap mass production and expensive case-by-case individualization, the Rotatable Mold is a compromise between two worlds: porcelain industry and porcelain artisanship. Porcelain production in small batches is called slip casting. This is easy to achieve with plaster molds, but has a decisive disadvantage: only the outer shape of a product can be designed. In order to define the inner form as well, a different process is required: solid casting. The necessary pressure-casting machines have been used in the porcelain industry for decades – but only in large-scale production. In Japan I got to know another – small-series – type of pressure-casting. It does not work with plastic molds as in industry, but with cheap plaster molds. It is highly customisable and requires only low pressure.
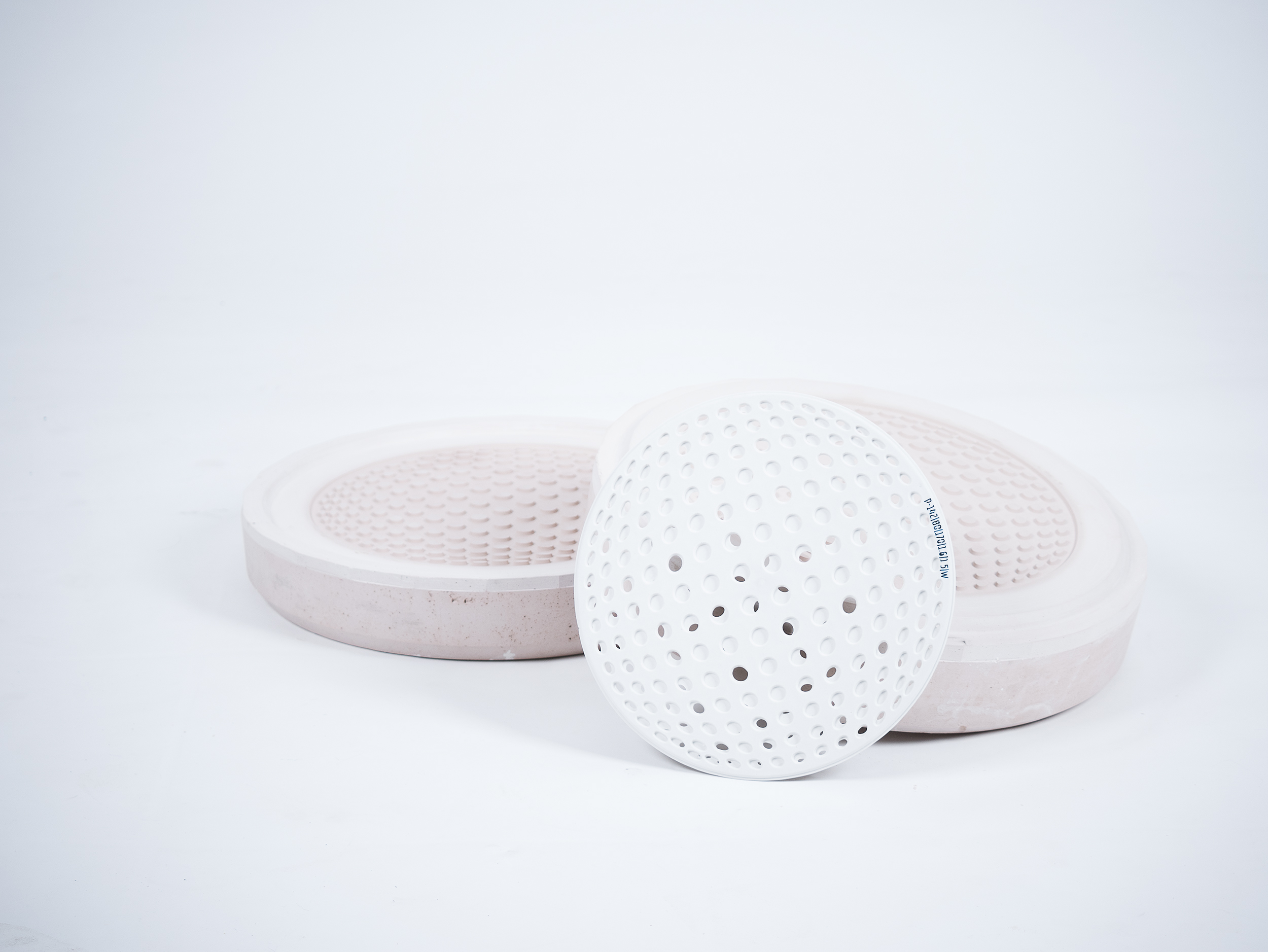
M3: Machine – Mass – Mold, design: Lotte Schloer / from designer’s archive
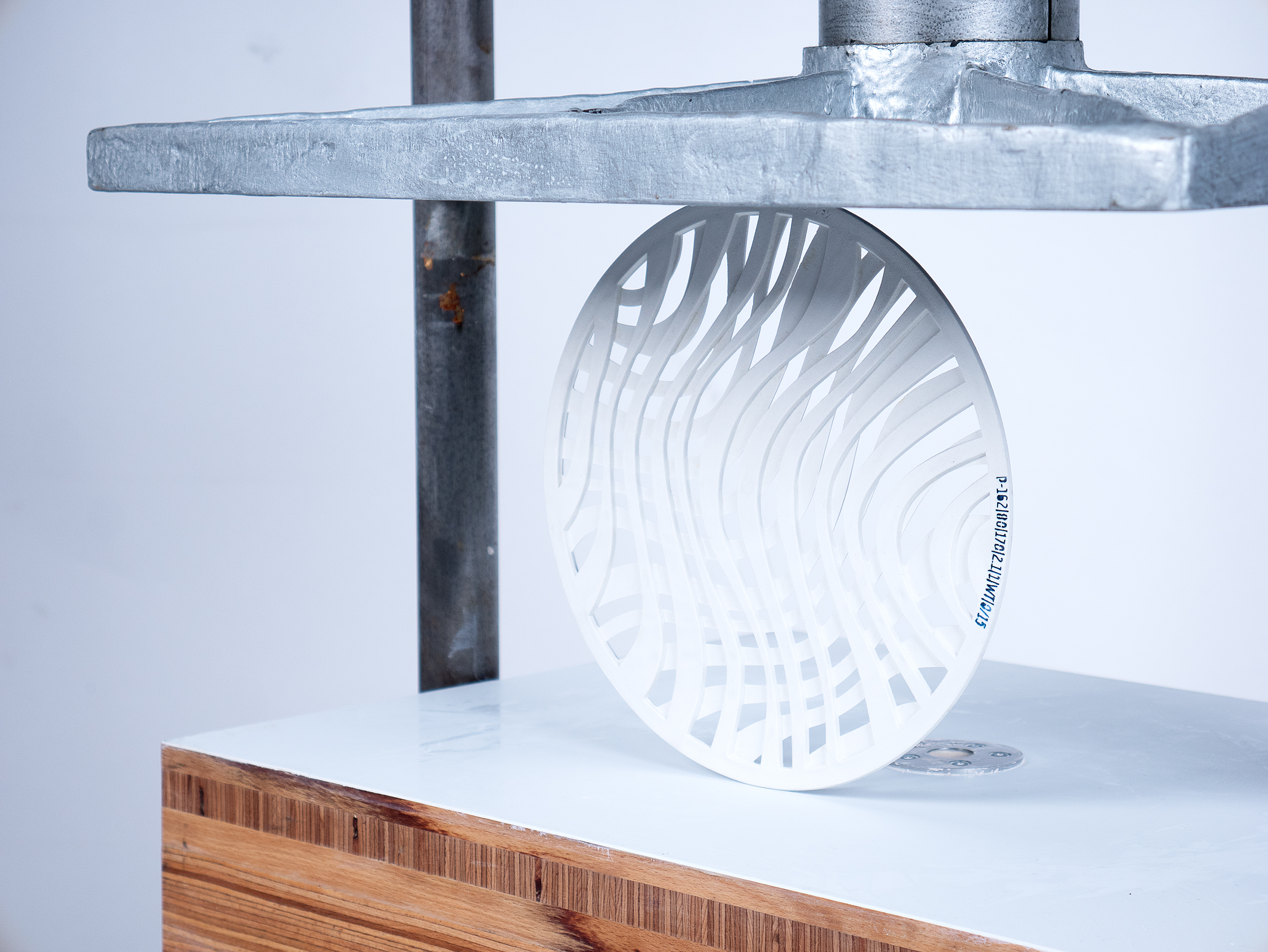
M3: Machine – Mass – Mold, design: Lotte Schloer / from designer’s archive
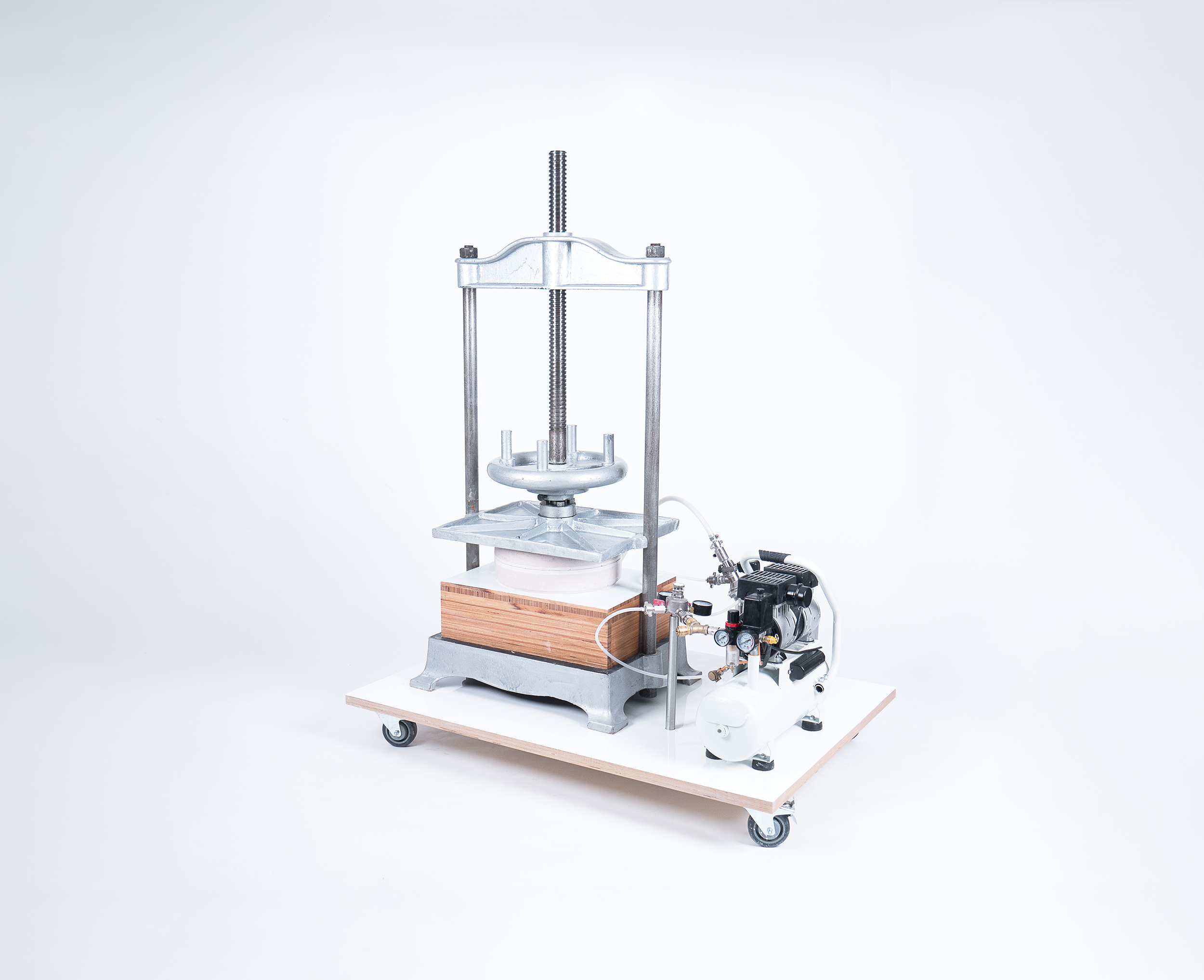
M3: Machine – Mass – Mold, design: Lotte Schloer / from designer’s archive
Lotte Schloer
I studied industrial design with a focus on ceramics and glass in Halle, Germany, and work as a porcelain designer in Munich, Halle, and Berlin. I started working with porcelain during my apprenticeship at the renown porcelain manufactory “Nymphenburg” in Munich, Bavaria. Here, I was trained as a professional porcelain painter for ancient and contemporary decors. After three years of intensive training, I started studying industrial design in the department of ceramics and glass at “Burg Giebichenstein” in Halle (Saale). Pursuing my passion for porcelain, the “White Gold”, I enhanced my previous 2D-skills with conceptualizing, prototyping, and promoting complex 3D-forms. My work is influenced by frequent international exchange (working trips to Estonia, Russia, Austria, France, etc.) as well as an international semester at Saga University, Arita, Japan. For the last four years, I have been frequently visiting national and international fairs, exhibitions, and gathering – seeking for inspiration or when exhibiting myself. I also took part in residencies and trainings, for example, a 3D printing workshop in Tallinn and an international artist tandem in Neumünster. Passionate about porcelain, I am always looking for contemporary approaches to one of the most fascinating materials in product design.
DESIGNER’S PORTFOLIO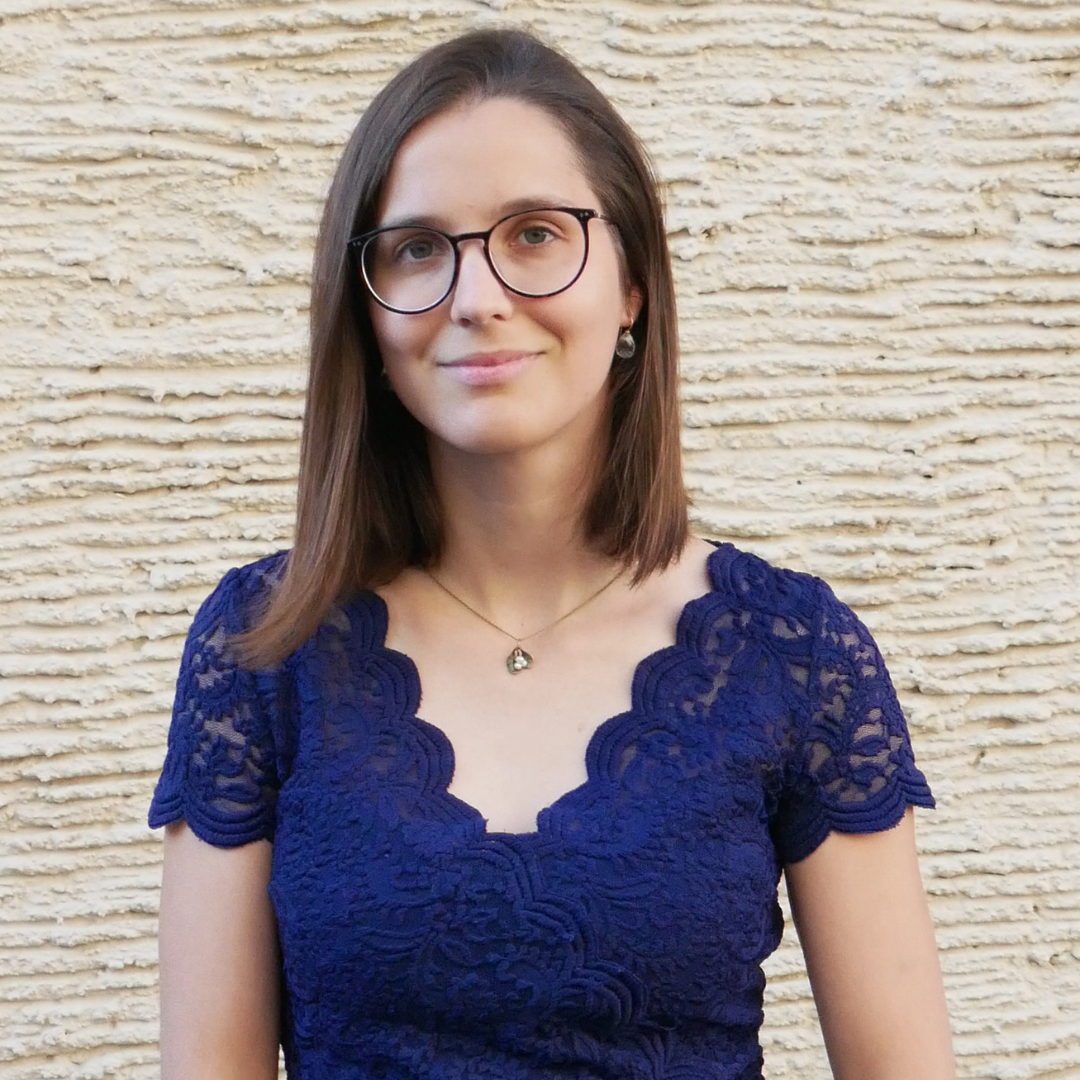